машина для обработки резанием металлических и др. материалов, полуфабрикатов или заготовок с целью получения из них изделий путём снятия стружки металлорежущим инструментом (См.
Металлорежущий инструмент)
.
М. с. являются основным видом оборудования в машиностроении, приборостроении и др. отраслях промышленности. Совершенствование М. с. предопределяет научно-технический прогресс, развитие технологии и организации машиностроительного производства.
Историческая справка. Обработка материалов резанием известна с древних времён: деталь вращали вручную, обработка велась кремнёвым резцом. В 12 в. появились токарные и сверлильные станки с ручным приводом, а в 14 в. - с приводом от водяных мельниц. Механические станки для токарных работ изготовлялись главным образом в Италии, Франции, откуда были завезены в Россию. Медальерными станками славились петербургские мастера. В 1711 в Россию из Флоренции привезли
станок, сделанный мастером Зингером, приглашенным на службу Петром I. В придворной токарне были изготовлены станки, в разработке конструкций и создании которых принимал участие А. К.
Нартов. Позднее Нартов построил другие станки (гравёрные, копировальные, гильотинные), ему же принадлежит создание первого в мире токарно-винторезного станка с механическим суппортом и сменными зубчатыми колёсами (1738). Основные промышленные типы М. с. разрабатывались позднее (Г.
Модсли и др.) в Великобритании, первой вступившей на путь капиталистического развития. В дальнейшем конструкция их совершенствовалась в Германии, Франции, Швейцарии (точное станкостроение), позже (во 2-й половине 19 в.) в США (в частности, автоматические станки для массового производства). В России в 1712-14 на Тульском оружейном заводе мастер Я. Батищев создал прототип современных агрегатных станков для одновременного сверления 24 ружейных стволов, в 1714 В. И. Геннин построил на Олонецких заводах многопозиционный
станок. Значительный вклад в развитие конструкции М. с. внёс М. В.
Ломоносов, который в середине 18 в. построил и применил в своих мастерских оригинальные шлифовальные и др. станки. Вклад в создание новых конструкций станков внесли также рус. инженеры и изобретатели И. Осипов, М. Сидоров, И.
Ползунов, И.
Кулибин, П. Захаво (первые автоматы для нарезания резьбы, 1810), В. Игнатов, Г. Горохов. Но несмотря на отдельные выдающиеся изобретения, станкостроение в царской России развивалось медленно. Только после Великой Октябрьской социалистической революции в процессе индустриализации машиностроительные предприятия стали получать новые станки. В 1932 завод "Красный пролетарий" выпустил первый современный токарно-винторезный
станок. В 1933 основан Экспериментальный научно-исследовательский институт металлорежущих станков (ЭНИМС), где было начато проектирование новых типов станков, изготовление гамм станков токарных, револьверных, сверлильных, фрезерных и др. К 1970 в СССР освоено 1817 типоразмеров М. с. Годовой выпуск составил 230 тыс. станков.
Большая заслуга в развитии станкостроения в СССР принадлежит советским учёным В. И. Дикушину, Н. С. Ачеркану, Д. Н. Решетову, А. П. Владзиевскому, Б. С. Балакшину, Г. М. Головину, Г. А. Шаумяну, В. С. Васильеву, А. С. Проннкову, В. А. Кудинову, А. С. Бриткину, Б. Л. Богуславскому, конструкторам Н. А. Волчеку, В. Н. Кедринскому, И. А. Ростовцеву, Ю. Б. Эрпшеру и др.
Совершенствование производства М. с. идёт в нескольких направлениях. Намечается увеличение выпуска агрегатных автоматических и полуавтоматических М. с. и автоматических линий. обеспечивающих автоматизацию технологических процессов в крупносерийном и массовом производстве (в СССР выпуск таких М. с. за период 1966-70 увеличился на 22,6\% при общем росте выпуска М. с. за этот период на 12\%). В 1973 выпущено 211 тыс. М. с. Перспективно освоение прецизионных станков (См.
Прецизионный станок)
, обусловливающих высокую точность и качество обработки деталей. Предусматривается дальнейшее расширение производства М. с. с числовым программным управлением (ЧПУ) для обеспечения автоматизации механической обработки изделий в индивидуальном и серийном производстве. В 1968-70 в серийном производстве освоено 23 типоразмера таких станков, в 1970 - 15 типов опытных образцов; их выпуск в 1973 составил 3800 шт. Внедрение М. с. с использованием адаптивных систем управления (см.
Самоприспосабливающаяся система) открывает новые пути повышения точности обработки и производительности. Для удовлетворения разнообразных потребностей народного хозяйства намечается увеличение числа типов тяжёлых уникальных станков. К 1970 создано около 500 типов тяжёлых уникальных М. с.
Классификация М. с. По специализации различают М. с. универсальные для выполнения разнообразных операций на изделиях широкой номенклатуры; широкого назначения для выполнения ограниченного числа операций на изделиях широкой номенклатуры; специализированные для обработки однотипных изделий разных размеров; специальные для обработки изделий одного типоразмера; агрегатные - специальные, состоящие из нормализованных деталей, узлов, силовых головок.
М. с. могут быть с ручным управлением (загрузка и установка заготовок, пуск, переключение режима обработки, холостые движения, снятие изделия - вручную), а также иметь различную степень автоматизации: полуавтоматы (установка заготовок, пуск, снятие изделия - вручную, остальные движения цикла обработки - автоматически),
Автоматы
(все рабочие и холостые движения производятся автоматически, человек осуществляет контроль за циклом работы); могут составлять автоматические линии (См.
Автоматическая линия)
(группа автоматов, объединённая системой транспортировки заготовок от одного к другому); иметь числовое программное управление (все рабочие и холостые движения обеспечиваются заранее закодированной программой, введённой в М. с. и посылающей преобразованные импульсы на исполнительные и управляющие механизмы).
Классификация металлорежущих станков
--------------------------------------------------------------------------------------------------------------------------------------------------------------------------------------------------------------------------------------------------------------------
| Номер | Наименова- | Типы станков |
| группы | ние группы |-----------------------------------------------------------------------------------------------------------------------------------------------------------------------------------------------------------------------------|
| станков | станков | 1 | 2 | 3 | 4 | 5 | 6 | 7 | 8 | 9 |
|-------------------------------------------------------------------------------------------------------------------------------------------------------------------------------------------------------------------------------------------------------------------|
| | | Автоматы и полуавтоматы | | | | | | | |
|-------------------------------------------------------------------------------------------------------------------------------------------------------------------------------------------------------------------------------------------------------------------|
| 1 | Токарные | одношпин- | многошпин- | Револьверные | Сверлильно- | Карусельные | Токарно- | Много- | Специализи- | Разные |
| | | дельные | дельные | | отрезные | | винторезные | резцовые | рованные для | токарные |
| | | | | | | | и лобовые | | фасонных | |
| | | | | | | | | | изделий | |
|-------------------------------------------------------------------------------------------------------------------------------------------------------------------------------------------------------------------------------------------------------------------|
| | | | Полуавтоматы | | | | | | |
|-------------------------------------------------------------------------------------------------------------------------------------------------------------------------------------------------------------------------------------------------------------------|
| 2 | Сверлильные | Вертикально- | одношпин- | многошпин- | Координатно- | Радиально- | Расточные | Алмазно- | Горизонтально- | Разные |
| | и расточные | сверлильные | дельные | дельные | расточные | сверлильные | | расточные | сверлильные | сверлильные |
|-------------------------------------------------------------------------------------------------------------------------------------------------------------------------------------------------------------------------------------------------------------------|
| 3 | Шлифоваль- | Круглошлифо- | Внутришлифо- | Обдирочно- | Специализи- | - | Заточные | Плоскошлифо- | Притирочные | Разные |
| | ные и | вальные | вальные | шлифовальные | рованные | | | вальные | и полиро- | станки |
| | доводочные | | | | шлифовальные | | | | вальные | работающие |
| | | | | | | | | | | абразивом |
|-------------------------------------------------------------------------------------------------------------------------------------------------------------------------------------------------------------------------------------------------------------------|
| 4 | Комбини- | - | - | - | - | - | - | - | - | - |
| | рованные | | | | | | | | | |
|-------------------------------------------------------------------------------------------------------------------------------------------------------------------------------------------------------------------------------------------------------------------|
| 5 | Зубо- и | Зубостро- | Зуборезные | Зубофрезер- | Зубофре- | Для | Резьбо- | Зубоотде- | Зубо- и | Разные |
| | резьбо- | гальные для | для кони- | ные для | зерные для | обработки | фрезерные | лочные | резьбо- | зубо- и |
| | обраба- | цилиндри- | ческих колёс | цилиндри- | червячных | торцов зубьев | | | шлифоваль- | резьбо- |
| | тывающие | ческих колёс | | ческих колёс | колёс | колёс | | | ные | обрабаты- |
| | | | | и шлицевых | | | | | | вающие |
| | | | | валов | | | | | | |
|-------------------------------------------------------------------------------------------------------------------------------------------------------------------------------------------------------------------------------------------------------------------|
| 6 | Фрезерные | Вертикально- | Фрезерные | - | Копироваль- | Вертикальные | Продольные | Широко- | Горизонталь- | Разные |
| | | фрезерные | непрерывного | | ные и | бесконсоль- | | универсаль- | ные | фрезерные |
| | | консольные | действия | | гравироваль- | ные | | ные | консольные | |
| | | | | | ные | | | | | |
|-------------------------------------------------------------------------------------------------------------------------------------------------------------------------------------------------------------------------------------------------------------------|
| | | Продольные | | | | | | | |
|-------------------------------------------------------------------------------------------------------------------------------------------------------------------------------------------------------------------------------------------------------------------|
| 7 | Строгальные, | одностоечные | двухстоечные | Поперечно- | Долбёжные | Протяжные | - | Протяжные | - | Разные |
| | долбёжные и | | | строгальные | | горизонталь- | | вертикальные | | строгальные |
| | протяжные | | | | | ные | | | | |
|-------------------------------------------------------------------------------------------------------------------------------------------------------------------------------------------------------------------------------------------------------------------|
| | | | Отрезные | | Пилы | | |
|-------------------------------------------------------------------------------------------------------------------------------------------------------------------------------------------------------------------------------------------------------------------|
| 8 | Разрезные | работающие | работающие | работающие | правильно- | ленточные | дисковые | ножовочные | - | - |
| | | токарным | абразивным | гладким или | отрезные | | | | | |
| | | резцом | кругом | насеченным | | | | | | |
| | | | | диском | | | | | | |
|-------------------------------------------------------------------------------------------------------------------------------------------------------------------------------------------------------------------------------------------------------------------|
| 9 | Разные | Муфто- и | Пилонасека- | Правильно- и | Балансиро- | Для | Делительные | - | - | - |
| | | трубообраба- | тельные | бесцентрово- | вочные | испытания | машины | | | |
| | | тывающие | | обдирочные | | инструмента | | | | |
--------------------------------------------------------------------------------------------------------------------------------------------------------------------------------------------------------------------------------------------------------------------
По точности различают 5 классов М. с.: Н - нормальной точности (например, большинство универсальных М. с.), П - повышенной точности (на базе Н), В - высокой точности, А - особо высокой точности (прецизионные), С - особо точные, или мастер-станки.
По массе М. с. бывают лёгкие (до 1 т), средние (до 10 т), тяжёлые (свыше 10 т), уникальные (свыше 100 т).
В зависимости от характера выполняемых работ и применяемого режущего инструмента в СССР принята единая система классификации и условного обозначения М. с. (табл.), разработанная в ЭНИМС. Все М. с. делятся на группы, которые, в свою очередь, разбиваются на типы. По этой классификации каждому М. с. серийного производства присваивается шифр (индекс), который образуется, как правило, числом из 3 или 4 цифр; первая цифра указывает группу, вторая - тип, третья и четвёртая характеризуют важнейшие размеры М. с. или обрабатываемого на нём изделия. Например, шифр 2150 обозначает вертикально-сверлильный
станок с максимальным диаметром сверления 50
мм. После модернизации М. с. в его шифр за первой цифрой добавляется какая-либо буква. Например, шифр 1К62 обозначает модернизированный токарно-винторезный
станок с высотой центров 200
мм. Модификация (видоизменение) базовой модели обозначается введением какой-либо буквы в конце шифра. Например, 6Н12К обозначает модификацию модернизированного консольного вертикально-фрезерного станка. Описание типов станков см. в статьях:
Зубообрабатывающий станок, Карусельный станок, Токарный станок, Сверлильный станок, Фрезерный станок, Шлифовальный станок.
Кинематика М. с. При обработке на М. с. очертания, форма деталей (производящие линии) образуется в результате согласованных между собой вращательных и прямолинейных движений заготовки и режущей кромки металлорежущего инструмента. Эти движения, называемые рабочими, могут быть простыми и сложными. В М. с. используются 4 метода получения производящих линий: копирование, огибание (обкатка), методы следа и касания. При копировании форма режущей кромки инструмента совпадает с формой производящей линии (рис. 1, а, б); при огибании производящая линия возникает в форме огибающей ряда последовательных положений режущей кромки инструмента, движущегося относительно заготовки (рис. 1, б); при методе следа производящая линия образуется как след движения точки режущей кромки инструмента (рис. 1, г, д), при методе касания производящая линия является касательной к ряду геометрических вспомогательных линий, образованных реальной точкой (вершиной) движущейся режущей кромки инструмента (рис. 1, е).
Рабочие движения в М. с. - главное движение и движение подачи. Главное движение, происходящее в направлении вектора скорости резания, обеспечивает отделение стружки от заготовки, а движение подачи - последовательное внедрение инструмента в заготовку, "захват" новых, ещё не обработанных участков. Главное движение в зависимости от типа М. с. может совершаться как заготовкой (токарные, продольно-строгальные и др. станки), так и инструментом (сверлильные, поперечно-строгальные, долбёжные, протяжные, фрезерные, шлифовальные и др. станки); это движение может быть вращательным (токарные, сверлильные, фрезерные, шлифовальные и др. М. с.) или поступательным (строгальные, долбёжные, протяжные и др. М. с.). Помимо рабочих движений, на М. с. совершаются также установочные и делительные движения, которые не используются в процессе обработки резанием, однако необходимы для осуществления полного технологического цикла. Все движения в М. с. обеспечивают соответствующие механизмы, в которые входят различные передачи: ремённые, зубчатые, червячные, реечные, винтовые, кулачковые, фрикционные и др. Эти передачи сочленяются между собой в определённой последовательности и образуют кинематические цепи, совокупность которых составляет кинематическую схему М. с. При этом пользуются условными обозначениями элементов и механизмов М. с. по ГОСТ 3462-61. На кинематических схемах указываются диаметры шкивов (D1, D2 и т.д.), числа зубьев зубчатых и червячных колёс (z1, z2 и т.д.), шаги винтов, заходности червяков и винтов, модули (т) некоторых зубчатых колёс (обычно находящихся в зацеплении с рейками), передаточные отношения плеч рычагов, характеристики звеньев настройки и др.
Для станков с вращательным главным рабочим движением скорость резания определяется по формуле:
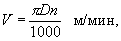
где
D - максимальный диаметр обработки (или максимальный диаметр инструмента) в
мм; n - число оборотов шпинделя в минуту. Для конкретного М. с. диаметр заготовки (инструмента) может быть различным, может производиться также обработка заготовок из различных материалов и режущими инструментами с режущей частью из разных инструментальных материалов (что приводит к выбору соответствующих допускаемых скоростей резания). Привод главного движения должен обеспечивать поэтому регулирование числа оборотов шпинделя. Существует бесступенчатое и ступенчатое регулирование. В первом случае в определённом интервале можно за счёт фрикционного, гидравлического или электрического привода получить любое значение
n. Во втором случае имеется определённый конечный ряд различных
n. Это обеспечивается за счёт использования коробок скоростей (См.
Коробка скоростей) с переключающимися зубчатыми колёсами. Для такого ряда рус. учёным А. В. Гадолиным в 1876 разработана и обоснована теория построения рядов чисел оборотов по закону геометрической прогрессии. При такой закономерности потери в устанавливаемых скоростях резания будут минимальными, а эксплуатационные свойства станка наилучшими. По этому закону все числа оборотов шпинделя станка в минуту от начального (миним.)
n1 =
nмин до конечного (макс.)
nz=
nмакс образуют геометрический ряд, в котором знаменатель геометрической прогрессии φ определяется по формуле:
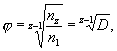
где D диапазон регулирования числа оборотов шпинделя в 1 мин, z - количество ступеней регулирования. В станкостроении СССР значения φ и соответствующие им перепады скоростей А стандартизированы:
------------------------------------------------------------------------------------------------------------------------------------------------------
| φ | 1,06 | 1,12 | 1,26 | 1,41 | 1,58 | 1,78 | 2 |
| | | | 1,25 | 1,4 | 1,6 | | |
|----------------------------------------------------------------------------------------------------------------------------------------------------|
| А, \% | 5 | 10 | 20 | 30 | 40 | 45 | 50 |
------------------------------------------------------------------------------------------------------------------------------------------------------
Примечание. Во втором ряду указаны допускаемые округления.
Основной показатель любой кинематической цепи - общее передаточное отношение:
где nk и nн - числа оборотов соответственно конечного и начального звеньев в об/мин; U1, U2, U3 - передаточные отношения отдельных пар кинематической цепи. Значение Uoбщ позволяет определить значения конечных перемещении звеньев, связанных кинематической цепью, т. е. заготовки и режущего инструмента. Соответствующие функциональные связи называют уравнениями кинематического баланса. Эти уравнения в 20-30-е гг. 20 в. выведены советским учёным Г. М. Головиным, предложившим единые формулы настройки для всех станков.
Для вращающихся конечных звеньев уравнение кинематического баланса: nk = nн · Uoбщ; для вращающегося начального звена и поступательно-движущегося конечного: nн · Uoбщ · Н = sm мм/мин, 1об · Uoбщ · Н = s мм/об, где Н - величина хода кинематической пары, преобразующей вращательное движение в прямолинейное, равная перемещению прямолинейно движущегося звена за один оборот вращающегося звена (для токарного, сверлильного, фрезерного и др. станков).
Для М. с. с прямолинейным главным движением (строгальный, долбёжный, протяжный и др.) различаются рабочий ход, в течение которого происходит резание, и холостой (обратный) ход, в течение которого движущиеся части станка возвращаются в исходное положение. Скорость холостого хода Vx = Vp · X, где Vp - скорость рабочего хода; Х = 1,5... 2,5 - коэффициент, выбираемый в зависимости от типоразмера станка.
Рабочий и холостой ходы составляют двойной ход. Время двойного хода:
где L - длина хода (в мм). Число двойных ходов (в 1 мин):
Для токарного станка с простой кинематической схемой ступенчатого главного привода (рис. 2), согласно уравнению кинематического баланса, возможны следующие варианты числа оборотов шпинделя в 1 мин:
т. е. возможно 12 вариантов (η - коэффициент, учитывающий проскальзывание в ремённой передаче).
Для облегчения кинематических расчётов коробок скоростей применяется графоаналитический метод. Зависимость чисел оборотов и передаточных отношений изображается в виде графиков и структурных сеток.
Конструктивные особенности М. с. Все кинематические цепи и рабочие органы М. с. выполняются в виде конструктивных узлов (механизмов), состоящих из различных деталей. Узлы и детали М. с. можно разделить на 2 группы. Группа несущей и направляющей системы обеспечивает правильное направление прямолинейных и круговых перемещений узлов с изделиями и с режущими инструментами. К ней относятся станины и основания; детали и узлы для поддержания и обеспечения прямолинейных перемещений изделий (консоли, салазки столов, столы); детали и узлы для поддержания и обеспечения прямолинейных и качательных перемещении режущих инструментов (суппорты, салазки и поперечины суппортов, револьверные головки); детали и узлы для обеспечения вращения изделий и режущих инструментов (шпиндели, опоры шпинделей, планшайбы, вращающиеся колонны, задние бабки); детали и узлы для поддержания и направления вращающихся деталей М. с. (корпуса коробок скоростей, коробок подач и шпиндельных бабок). Группа привода и управления осуществляет формообразование деталей и движения управления. К ней относятся механизмы главного движения, движения подачи и делительных движений; механизмы вспомогательных движений (транспортирующих, зажимных, установочных, стружкоотводящих); механизмы управления (пуском и остановом, скоростью и реверсированием равномерных движений), копировальные, программные, адаптивные, самоподстраивающпеся системы. Конструктивные компоновки М. с. различных типов могут быть самыми различными в соответствии с рассмотренной ранее классификацией (рис. 3, а-т).
В развитии конструкций узлов М. с. существуют следующие тенденции: оптимальное использование возможностей механических, электрических и гидравлических приводов и их сочетаний; разработка прецизионных узлов и механизмов; уменьшение трения в узлах станков; применение средств управления и автоматизации; обеспечение высокой статической и динамической жесткости; повышение долговечности за счёт выбора оптимальных материалов и методов упрочнения деталей; применение унификации, нормализации, стандартизации и агрегатирования.
Надёжность М. с. Надёжность М. с. - его свойство выполнять заданные функции, т. е. обрабатывать изделия с сохранением в необходимых пределах эксплуатационных показателей, главным образом точности и производительности, в течение требуемого промежутка времени (наработки (См.
Наработка))
. Надёжность М. с. определяется его
Безотказностью
, Долговечностью
, Ремонтопригодностью и сохраняемостью.
На надёжность М. с. прежде всего влияют режимы и методы обработки, которые предопределяют точность и качество обработанных поверхностей, а следовательно, эксплуатационные характеристики изделий. Повышение надёжности М. с. обеспечивается увеличением точности изготовления М. с.; созданием специальных устройств для повышения точности обработки; применением систем автоматического регулирования для восстановления точности, снижающейся от действия процессов, протекающих с различной скоростью, т. е. создание М. с. с автоматической подналадкой режимов обработки. Системы автоматического регулирования - наиболее современный способ создания М. с. с высокой надёжностью. Автоматическое регулирование может быть простым по заданной программе; прямым с учётом факторов, вызывающих отклонение от программы; по замкнутому циклу с обратной связью. Последний способ приводит к созданию адаптивных саморегулирующихся (самоподстраивающихся) систем, дающих наибольшую надёжность М. с. Адаптивные системы управления М. с. разделяются на следующие группы: стабилизирующие контролируемые параметры резания; самоизменяющие управляющую программу; компенсирующие динамические и температурные деформации системы СПИД (станок - приспособление - инструмент - деталь); оптимизирующие режимы обработки по точности и производительности. Использование адаптивных систем управления М. с. обеспечивает снижение (и даже исключение) отказов из-за перегрузок, уменьшение зависимости результата обработки от рабочего, упрощение программирования обработки, автоматический контроль получаемых размеров деталей, повышение экономичности обработки, облегчение освоения новых методов обработки.
М. с. с числовым программным управлением. Числовое программное управление (ЧПУ) М. с. экономически выгодно в серийном производстве, где происходит сравнительно частая смена обрабатываемых изделий, а также при производстве крупногабаритных деталей и деталей с криволинейными профилями и поверхностями. ЧПУ позволяет автоматизировать процессы подготовки производства и обработки, быстро производить переналадку станка. В М. с. с ЧПУ информация о необходимых перемещениях режущих инструментов относительно заготовки сообщается механизмам управления М. с. в виде закодированной программы, представляющей собой условную систему числовых обозначений. Эта программа вводится в считывающее устройство М. с., которое преобразует её в соответствующие командные импульсы (электрические сигналы), а они при помощи механизмов управления передаются на исполнительные органы М. с. (суппорты, салазки, столы и т.п.). Все действия, выполняемые узлами М. с. по сигналам системы ЧПУ, разделяются на две группы: включения и выключения для изменения режимов резания, смены действующих режущих инструментов и т.п.; перемещения исполнительных органов.
Системы ЧПУ, применяемые в М. с., классифицируются: по назначению - для позиционного, ступенчатого и функционального управления; по числу потоков информации - разомкнутые, замкнутые и самонастраивающиеся; по виду программоносителя - внутренние (панели с переключателями, штеккерные и кнопочные панели и др.) и внешние (перфорированные карты и ленты, магнитные ленты, киноленты и др.); по принципу ограничения перемещений исполнительных органов - импульсные, аналоговые, путевые, временные, на схемах совпадения; по физическому принципу контроля перемещений исполнительных органов - с механическими, оптическими, электрическими и смешанными измерительными устройствами. Применяется также цикловая система программного управления, при которой программируются (полностью или частично) цикл работы М. с., режимы обработки и смена инструмента.
Системы ЧПУ М. с. состоят обычно из следующих основных автоматических элементов (рис. 4): устройство для ввода программы - "читает" программу и преобразовывает её в сигналы управления; промежуточная "память" - "запоминает" и в течение необходимого времени хранит полученные сигналы управления; сравнивающее устройство (узел активного контроля) - при помощи системы обратной связи сопоставляет перемещения, заданные программой и фактически реализованные М. с. (при обнаружении разницы вырабатывает дополнительный сигнал для исправления ошибки); исполнительный механизм, который реализует через соответствующие приводы (гидроцилиндры, винтовые пары, шаговые двигатели и др.) полученные сигналы управления в необходимые перемещения исполнительных органов М. с.
Лит.: Машиностроение. Энциклопедический справочник, т. 9, М., 1949; Шувалов Ю. А., Веденский В. А., Металлорежущие станки, 2 изд., М., 1959; 3агорский Ф. Н., Очерки по истории металлорежущих станков до середины XIX века, М. - Л., 1960; Металлорежущие станки, под ред. Н. С. Ачеркана, т. 1-2, М., 1965; Агурский М. С., Вульфсон И. А., Ратмиров В. А., Числовое программное управление станками, М., 1966; Шаумян Г. А., Кузнецов М. М., Волчкевич Л. И., Автоматизация производственных процессов, М., 1967; Резание конструкционных материалов, режущие инструменты и станки, М., 1967; Проников А. С., Расчёт и конструирование металлорежущих станков, 2 изд., М., 1967; Кучер И. М., Металлорежущие станки, 2 изд., Л., 1969; Самоподнастраивающиеся станки, [Сб. ст.1, под ред. Б. С. Балакшина, 3 изд., М., 1970; Налчан А. Г. (сост.), Металлорежущие станки, М., 1970; Металлорежущие станки, М., 1970; Ратмиров В. А., Сиротенко А. П., Гаевский Ю. С., Самонастраивающиеся системы управления станками, М., 1971; Технологическая надёжность станков, М., 1971; Детали и механизмы металлорежущих станков, под ред. Д. Н. Решетова, т. 1-2, М., 1972.
Д. Л. Юдин.
Рис. 3а. Основные типы металлорежущих станков. Зубошлифовальный станок (5853).
Рис. 3б. Основные типы металлорежущих станков. Зубострогальный полуавтомат (5А250П).
Рис. 3в. Основные типы металлорежущих станков. Хонинговальный вертикальный одношпиндельный станок (ЗБ833).
Рис. 3г. Основные типы металлорежущих станков. Станок для перешлифовки шатунных и коренных шеек коленчатых валов (3А423).
Рис. 3д. Основные типы металлорежущих станков. Координатно-расточный станок (2B440).
Рис. 3е. Основные типы металлорежущих станков. Радиально-сверлильный станок (2A53).
Рис. 3ж. Основные типы металлорежущих станков. Токарно-карусельный одностоечный станок с числовым программным управлением (1512Ф2).
Рис. 3з. Основные типы металлорежущих станков. Универсальный токарно-винторезный станок с автоматическим циклом (1K62A).
Рис. 3и. Основные типы металлорежущих станков. Зубофрезерный станок (5K328A).
Рис. 3к. Основные типы металлорежущих станков Зубодолбёжный полуавтомат (5122).
Рис. 3л. Основные типы металлорежущих станков. Внутришлифовальный станок (3260).
Рис. 3м. Основные типы металлорежущих станков. Круглошлифовальный автомат (3К161).
Рис. 3н. Основные типы металлорежущих станков. Вертикально-сверлильный станок (2A135).
Рис. 3о. Основные типы металлорежущих станков. Копировальный поперечно-строгальный станок (ГД-21).
Рис. 3п. Основные типы металлорежущих станков. Вертикально-протяжной станок (7Б705).
Рис. 3р. Основные типы металлорежущих станков. Токарный восьмишпиндельный автомат (1К282).
Рис. 3с. Основные типы металлорежущих станков. Вертикально-фрезерный станок с копировальным устройством (6Н12К).
Рис. 3. Основные типы металлорежущих станков. Универсальный консольно-фрезерный станок (6Т82).
Рис. 1. Воспроизведения производящих линий методом: а, б - копирования; в - огибания (обката); г, д - следа; е - касания; П - производящая линия.
Рис. 2. Кинематическая схема главного привода токарного станка.
Рис. 4. Структурная схема цифрового программного управления металлорежущего станка: 1 - устройство для ввода программы; 2 - промежуточная "память"; 3 - сравнивающее устройство; 4 - исполнительный механизм; 5 - узел обратной связи (активного контроля).